Working Principles of All Types of Shot Blasting Machines(Part One)
Since many people may not know much about shot blasting machines or have never heard of them, JX Abrasive has listed working principles of shot blasting machines for you.
1. What are functions of shot blasting machines?
(1) To remove rusty layer, welding slag, oxide scale, making product surface have even metallic luster.
(2) To form a rough surface, increasing the friction coefficient of components and improving the paint adhesion so as to improve coating quality and anti-corrosion of steels.
2. Working principle of blast wheel
An blast wheel is the main component of a shot blasting machine. An blast wheel consists of impeller wheel, shot wheel, control cage, spindle, etc. Iron shots fall into shot wheels by their weight, and shot wheels rotate along with iron shots at the same speed as spindles'.
Then the iron shots are pressed to the inside of control cages under the impact of centrifugal force. When the iron shots come to the square window of the control cage, they are thrown through the window and are caught by the blades rotating in high speed. Then they move outwards along the wheel blades at a accelerated speed. Finally, the iron shots are thrown to the castings in a fan-shaped curve at the speed of 60 to 80m/s, so as to clean up the casting surface.
By adjusting the window position of control cage, we can adjust the throwing direction of the iron shots, increasing the possibility for the castings to catch the iron shots. However, improperly setting the position of the control cage will decrease the shot blasting cleaning efficiency since the arc-shaped fender is severely abraded. The opening size of the control cage can affect the divergence angle of the iron shots(the fan-shaped included angle), that is, bigger opening makes divergence angle bigger, which will make the cleaning effect of shot blasting machine become worse. Given these factors, we should adjust the position of the control cage in time once it wears seriously and we even need to replace it with the new one when its abrasion loss is over 13mm.
The projection velocity and abrasive flow rate of iron shot are the main influencing factors of blast wheels' cleaning efficiency. When projection velocity gets higher, impact force becomes stronger. When the abrasive flow rate rises in unit time, the iron shot density also increases in the casting unit area.
Moreover, the distance from the blast wheel to the casting surface also affects the abrasive flow rate. After leaving the blast wheel the projection velocity of shots is decreased by air resistance. Generally, when the iron shot moves, about ten percent of its kinetic energy is lost per meter. Therefore, it is better to set the casting surface about 0.7m to 1.5m away from the center line of the blast wheel. The reason is the iron shot’s impact force will be too great if the surface and machine are too close with each other, but the cleaning performance will be decreased if the surface and machine are too far from each other.
1. What are functions of shot blasting machines?
(1) To remove rusty layer, welding slag, oxide scale, making product surface have even metallic luster.
(2) To form a rough surface, increasing the friction coefficient of components and improving the paint adhesion so as to improve coating quality and anti-corrosion of steels.
2. Working principle of blast wheel
An blast wheel is the main component of a shot blasting machine. An blast wheel consists of impeller wheel, shot wheel, control cage, spindle, etc. Iron shots fall into shot wheels by their weight, and shot wheels rotate along with iron shots at the same speed as spindles'.
Then the iron shots are pressed to the inside of control cages under the impact of centrifugal force. When the iron shots come to the square window of the control cage, they are thrown through the window and are caught by the blades rotating in high speed. Then they move outwards along the wheel blades at a accelerated speed. Finally, the iron shots are thrown to the castings in a fan-shaped curve at the speed of 60 to 80m/s, so as to clean up the casting surface.
By adjusting the window position of control cage, we can adjust the throwing direction of the iron shots, increasing the possibility for the castings to catch the iron shots. However, improperly setting the position of the control cage will decrease the shot blasting cleaning efficiency since the arc-shaped fender is severely abraded. The opening size of the control cage can affect the divergence angle of the iron shots(the fan-shaped included angle), that is, bigger opening makes divergence angle bigger, which will make the cleaning effect of shot blasting machine become worse. Given these factors, we should adjust the position of the control cage in time once it wears seriously and we even need to replace it with the new one when its abrasion loss is over 13mm.
The projection velocity and abrasive flow rate of iron shot are the main influencing factors of blast wheels' cleaning efficiency. When projection velocity gets higher, impact force becomes stronger. When the abrasive flow rate rises in unit time, the iron shot density also increases in the casting unit area.
Moreover, the distance from the blast wheel to the casting surface also affects the abrasive flow rate. After leaving the blast wheel the projection velocity of shots is decreased by air resistance. Generally, when the iron shot moves, about ten percent of its kinetic energy is lost per meter. Therefore, it is better to set the casting surface about 0.7m to 1.5m away from the center line of the blast wheel. The reason is the iron shot’s impact force will be too great if the surface and machine are too close with each other, but the cleaning performance will be decreased if the surface and machine are too far from each other.
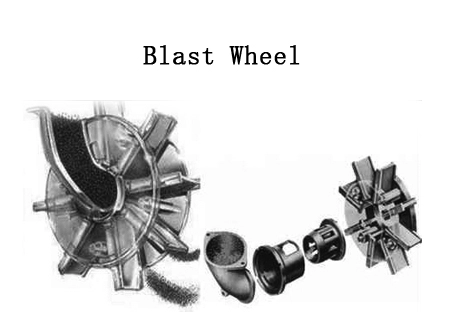